As the main power source of new energy vehicles, power batteries are of great importance to new energy vehicles. During the actual use of the vehicle, the battery will face complex and changeable working conditions.
At low temperature, the internal resistance of lithium-ion batteries will increase and the capacity will decrease. In extreme cases, the electrolyte will freeze and the battery cannot be discharged. The low-temperature performance of the battery system will be greatly affected, resulting in the power output performance of electric vehicles. Fade and range reduction. When charging new energy vehicles under low temperature conditions, the general BMS first heats the battery to a suitable temperature before charging. If it is not handled properly, it will lead to instantaneous voltage overcharge, resulting in internal short circuit, and further smoke, fire or even explosion may occur.
At high temperature, if the charger control fails, it may cause a violent chemical reaction inside the battery and generate a lot of heat. If the heat accumulates quickly inside the battery without time to dissipate, the battery may leak, outgas, smoke, etc. In severe cases, the battery will burn violently and explode.
The battery thermal management system (Battery Thermal Management System, BTMS) is the main function of the battery management system. The thermal management of the battery mainly includes the functions of cooling, heating and temperature equalization. The cooling and heating functions are mainly adjusted for the possible impact of the external ambient temperature on the battery. Temperature equalization is used to reduce the temperature difference inside the battery pack and prevent rapid decay caused by overheating of a certain part of the battery. A closed-loop regulation system is composed of heat-conducting medium, measurement and control unit, and temperature control equipment, so that the power battery can work within a suitable temperature range to maintain its optimal use state and ensure the performance and life of the battery system.
1. "V" model development mode of thermal management system
As a component of the power battery system, the thermal management system is also developed in accordance with the V" model development model of the automotive industry. With the help of simulation tools and a large number of test verifications, only in this way can the development efficiency be improved, the development cost and the guarantee system be saved. Reliability, safety and longevity.
The following is the "V" model of thermal management system development. Generally speaking, the model consists of two axes, one horizontal and one vertical: the horizontal axis is composed of four main lines of forward development and one main line of reverse verification, and the main line is forward development. , taking into account the reverse closed-loop verification; the vertical axis consists of three levels: components, subsystems and systems.
The temperature of the battery directly affects the safety of the battery, so the design and research of the thermal management system of the battery is one of the most critical tasks in the design of the battery system. The thermal management design and verification of the battery system must be carried out in strict accordance with the battery thermal management design process, battery thermal management system and component types, thermal management system component selection, and thermal management system performance evaluation. In order to ensure the performance and safety of the battery.
1. Requirements of the thermal management system. According to the design input parameters such as the use environment of the vehicle, the operating conditions of the vehicle, and the temperature window of the battery cell, conduct demand analysis to clarify the requirements of the battery system for the thermal management system; system requirements, according to Requirements analysis determines the functions of the thermal management system and the design goals of the system. These design goals mainly include the control of battery cell temperature, temperature difference between battery cells, system energy consumption and cost.
2. Thermal management system framework. According to system requirements, the system is divided into cooling subsystem, heating subsystem, thermal insulation subsystem and thermal runaway obstructin (TRo) subsystem, and the design requirements of each subsystem are defined. At the same time Simulation analysis is carried out to initially verify the system design. Such as PTC cooler heater, PTC air heater, electronic water pump, etc.
3. Subsystem design, first determine the design goal of each subsystem according to the system design, and then carry out method selection, scheme design, detailed design and simulation analysis and verification for each subsystem in turn.
4. Parts design, first determine the design objectives of the parts according to the subsystem design, and then carry out detailed design and simulation analysis.
5. Manufacturing and testing of parts, manufacturing of parts, and testing and verification.
6. Subsystem integration and verification, for subsystem integration and test verification.
7. System integration and testing, system integration and testing verification.
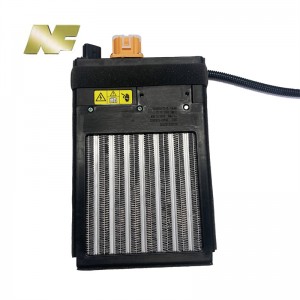
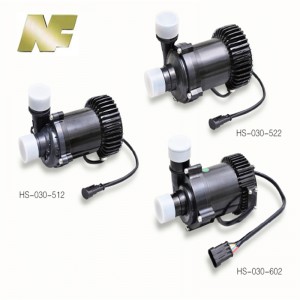
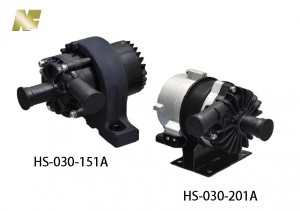
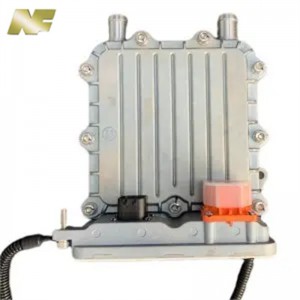
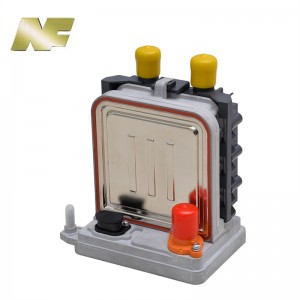
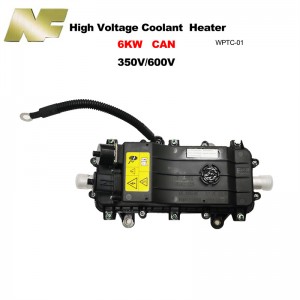
Post time: Jun-02-2023