The thermal management of the automotive power system is divided into the thermal management of the traditional fuel vehicle power system and the thermal management of the new energy vehicle power system. Now the thermal management of the traditional fuel vehicle power system is very mature. The traditional fuel vehicle is powered by the engine, so the engine Thermal management is the focus of traditional automotive thermal management. The thermal management of the engine mainly includes the cooling system of the engine. More than 30% of the heat in the car system needs to be released by the engine cooling circuit to prevent the engine from overheating under high-load operation. The engine's coolant is used to heat the cabin.
The power plant of traditional fuel vehicles is composed of engines and transmissions of traditional fuel vehicles, while new energy vehicles are composed of batteries, motors, and electronic controls. The thermal management methods of the two have undergone great changes. The power battery of new energy vehicles The normal working temperature range is 25~40℃. Therefore, thermal management of the battery requires both keeping it warm and dissipating it. At the same time, the temperature of the motor should not be too high. If the temperature of the motor is too high, it will affect the service life of the motor. Therefore, the motor also needs to take necessary heat dissipation measures during use. The following is an introduction to the thermal management system of the battery and the thermal management system of the motor electronic control and other components.
Power battery thermal management system
The thermal management system of the power battery is mainly divided into air cooling, liquid cooling, phase change material cooling and heat pipe cooling based on different cooling media. The principles and system structures of different cooling methods are quite different.
1) Power battery air cooling: the battery pack and the outside air conduct convective heat exchange through the flow of air. Air cooling is generally divided into natural cooling and forced cooling. Natural cooling is when the outside air cools the battery pack when the car is running. Forced air cooling is to install a fan for forced cooling against the battery pack. The advantages of air cooling are low cost and easy commercial application. The disadvantages are low heat dissipation efficiency, large space occupation ratio, and serious noise problems.(PTC Air Heater)
2) Power battery liquid cooling: the heat of the battery pack is taken away by the flow of liquid. Since the specific heat capacity of liquid is larger than that of air, the cooling effect of liquid cooling is better than that of air cooling, and the cooling speed is also faster than that of air cooling, and the temperature distribution after heat dissipation of the battery pack is relatively uniform. Therefore, liquid cooling is also widely used commercially.(PTC Coolant Heater)
3) Cooling of phase change materials: Phase change materials (PhaseChangeMaterial, PCM) include paraffin, hydrated salts, fatty acids, etc., which can absorb or release a large amount of latent heat when a phase change occurs, while their own temperature remains unchanged. Therefore, PCM has a large thermal energy storage capacity without additional energy consumption, and is widely used in battery cooling of electronic products such as mobile phones. However, the application of automotive power batteries is still in the research state. Phase change materials have the problem of low thermal conductivity, which causes the surface of PCM in contact with the battery to melt, while other parts do not melt, which reduces the heat transfer performance of the system and is not suitable for large-sized power batteries. If these problems can be solved, PCM cooling will become the most potential development solution for thermal management of new energy vehicles.
4) Heat pipe cooling: A heat pipe is a device based on phase change heat transfer. A heat pipe is a sealed container or sealed pipe filled with a saturated working medium/liquid (water, ethylene glycol, or acetone, etc.). One section of the heat pipe is the evaporation end, and the other end is the condensation end. It can not only absorb the heat of the battery pack but also heat the battery pack. It is currently the most ideal power battery thermal management system. However, it is still under research.
5) Refrigerant direct cooling: direct cooling is a way to use the principle of R134a refrigerant and other refrigerants to evaporate and absorb heat, and install the evaporator of the air conditioning system in the battery box to quickly cool the battery box. The direct cooling system has high cooling efficiency and large cooling capacity.
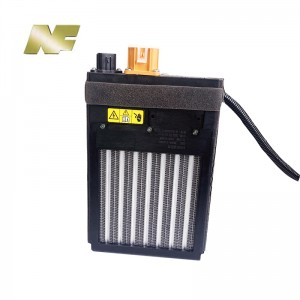
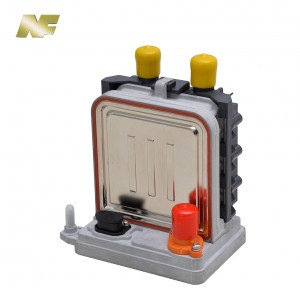
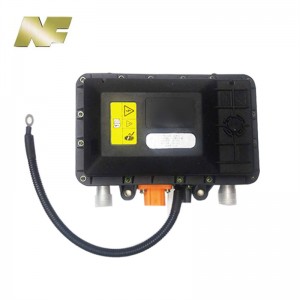
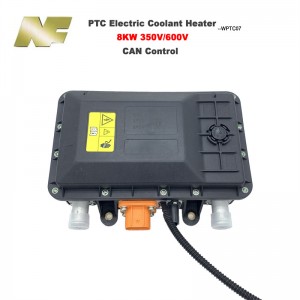
Post time: Apr-29-2024