liquid medium heating
Liquid heating is generally used in the liquid medium thermal management system of the vehicle. When the vehicle battery pack needs to be heated, the liquid medium in the system is heated by the circulation heater, and then the heated liquid is delivered to the cooling pipeline of the battery pack. Using this heating method to heat the battery has high heating efficiency and heating uniformity. Through a reasonable circuit design, the heat of each part of the vehicle system can be effectively exchanged to achieve the purpose of energy saving.
This heating method is the one with the lowest energy consumption among the three battery heating methods. Since this heating method needs to cooperate with the vehicle's liquid medium thermal management system, the design is difficult and there is a certain risk of liquid leakage. Currently, the utilization rate of this heating solution is lower than that of the electric heating film heating method. However, it has great advantages in energy consumption and heating performance, and will become the development trend of electric vehicle battery thermal management systems in the future. Typical representative product: PTC Coolant Heater.
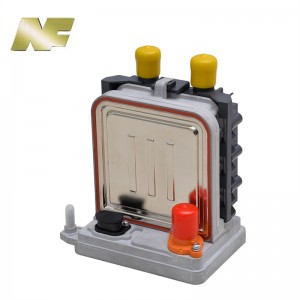
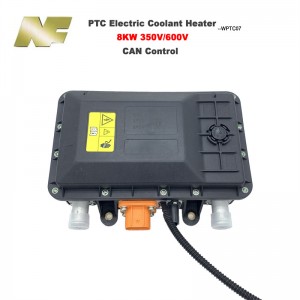
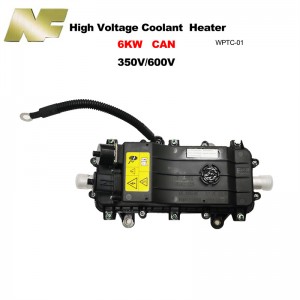
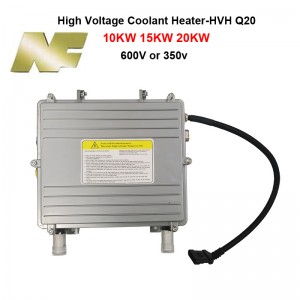
Optimizing Prospects in Low Temperature Conditions
the problem we are facing
Battery activity decreases under low temperature conditions
Lithium batteries migrate between the positive and negative electrodes through lithium ions to complete the charging and discharging process of the battery. Studies have shown that in low temperature environments, the discharge voltage and discharge capacity of lithium-ion batteries are significantly reduced. At −20°C, the discharge capacity of the battery is only about 60% of the normal condition. Under low temperature conditions, the charging power will also drop, and the charging time will be longer.
Cold car restart power off
Under most operating conditions, parking in a low-temperature environment for a long time will cause the complete vehicle system to cool down completely. When the vehicle is started again, the battery and the cockpit will not meet the optimum operating temperature. Under low temperature conditions, the activity of the battery decreases, which not only affects the cruising range and output power of the vehicle, but also limits the maximum discharge current, which poses a safety hazard to the vehicle.
Solution
Brake heat recovery
When the car is running, especially when driving vigorously, the brake disc in the braking system will generate more heat due to friction. Most high-performance cars have brake air ducts for good cooling. The brake air guide system guides the cold air in front of the vehicle through the air guide slots in the front bumper to the brake system. The cold air flows through the interlayer gap of the ventilated brake disc to take away the heat from the brake disc. This part of the heat is lost in the external environment and is not fully utilized.
In the future, a heat collection structure can be used. Copper heat dissipation fins and heat pipes are placed inside the wheel arches of the vehicle to collect the heat generated by the braking system. After cooling the brake discs, the heated hot air passes through the fins and heat pipes to transfer the heat The heat is transferred to an independent circuit, and then the heat is introduced into the heat exchange process of the heat pump system through this circuit. While cooling the brake system, this part of waste heat is collected and utilized to heat and keep the battery pack warm.
As an important hub of electric vehicles, the electric vehicle thermal management system manages the PTC air conditioning, energy storage, drive and heat exchange between the cabins of the vehicle, which plays an important role in the design of the vehicle. When designing the battery thermal management system, it is necessary to control costs while taking into account various environments and working conditions to ensure that all components of the vehicle are at an appropriate operating temperature. The existing battery thermal management system can meet the temperature control requirements of the battery under most working conditions, but in terms of energy utilization, energy saving, low temperature working conditions, etc., the thermal insulation performance of the battery needs to be improved and perfected.
Post time: May-19-2023