Although the fuel cell is still mainly on commercial vehicles, passenger cars are only Toyota Honda Hyundai has products, but because the article focuses on passenger cars, and other comparison models are also passenger cars, so here is the Toyota Mirai as an example.
The fuel cell thermal management system features the following three main points:
Fuel cell reactor heat dissipation requirements
The reactor is the site of the hydrogen-oxygen reaction and generates heat while producing electricity. The increase in temperature helps to increase the discharge power of the reactor, but the heat cannot be gathered, so the reaction product water and the reactor coolant need to flow together to dissipate the heat.
And maintaining the temperature of the reactor can effectively control the output power to meet the driver's dynamic needs for the drive system. The heat generated by the power electronics of the reactor and motor inverter can be used as part of the heat for cockpit heating in winter.
The problem of cold start of the reactor
The fuel cell reactor cannot provide electricity directly at low temperature, so it needs to be warmed up by external heat before it can enter normal operation mode.
At this point, the heat dissipation circuit mentioned above needs to be reversed to a heating circuit, and the switching here may require a circuit control valve similar to a three-way two-way valve.
Heating can be done by an external electric PTC heater, electric heating power from the battery to provide. It seems that there is also technology that allows the reactor to generate its own heat, so that the energy generated by the reaction is more in the form of heat to the body of the reactor to warm up.
Booster cooling
This part is a bit like the hybrid car party mentioned earlier, in order to meet the power demand of the reactor, the amount of reactant oxygen also has a certain demand, so the air intake needs to be pressurized to increase the density, thereby increasing the mass flow of oxygen. For this reason brings the post-boost cooling, which can be connected in series in the same cooling circuit since the temperature range is relatively close to the other components.
Pure Electric Vehicles
Written at the end of the day pure electric vehicles are the most popular players in the market today. Research and development in thermal management of electric vehicles has been done at all major car manufacturers and suppliers. The following are three main points where it differs from other vehicle types:
Winter range concerns
Most of the credit for range goes to battery energy density, vehicle electrical consumption, and wind resistance, which are non-thermal management aspects, but not so much in winter.
In order to meet the comfort in the cockpit and high voltage battery cold start, a lot of electrical energy is consumed by the thermal management system, and a significant reduction in winter range is already the norm.
The main reason is that the pure electric vehicle drive system heat generation is far more than the engine, the battery and temperature sensitive.
Currently common solutions such as heat pump system, the drive system heat and environmental heat through the compressor cycle to provide the cabin and battery, there is also the Weimar EX5 in the use of diesel heaters, the use of a portion of diesel combustion heat to provide the battery and cabin preheating(PTC heaters), there is another is the battery self-heating technology, so that when the battery is started with a small portion of energy to achieve the warming of each battery unit, thereby reducing reliance on external heat exchange circuits.
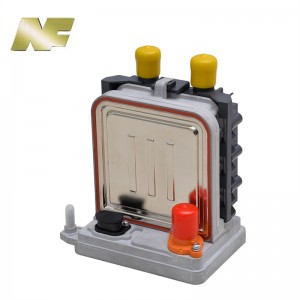
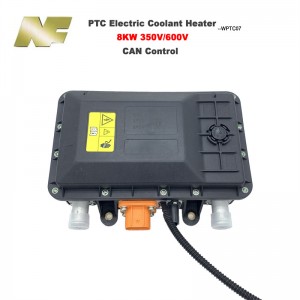
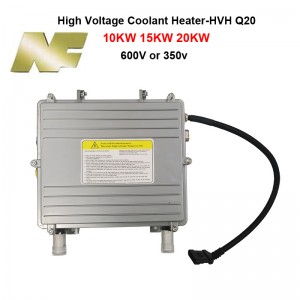
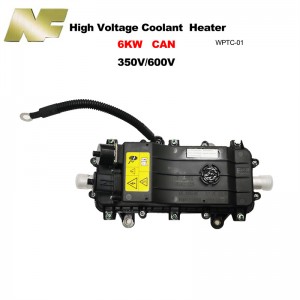
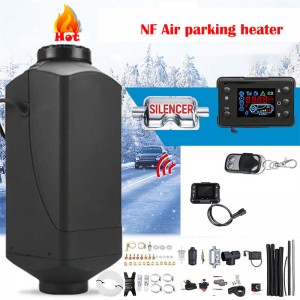
Post time: Apr-20-2023