As the market share of electric vehicles continues to increase, automakers are gradually shifting their R&D focus to power batteries and intelligent control. Due to the chemical characteristics of the power battery, temperature will have a greater impact on the charging and discharging performance and safety of the power battery. Therefore, in the development of electric vehicles, the design of the battery thermal management system has a higher priority. Based on the existing mainstream electric vehicle battery thermal management system structure, combined with Tesla's eight-way valve heat pump system technology, the working principle of the power battery and the advantages and disadvantages of the thermal management system are analyzed. There are problems such as cold car power loss, short cruising range, and reduced charging power, and an optimization scheme for the thermal management system of the power battery is proposed.
Due to the unsustainability of traditional energy sources and the increasing environmental pollution, governments and automobile manufacturers in various countries have accelerated the transformation to new energy vehicles, focusing on promoting the development of electric vehicles mainly driven by pure electricity. As the market share of electric vehicles continues to increase, power batteries and intelligent control are becoming the technological development trend of electric vehicles. No better solution was found. Different from traditional gasoline vehicles, electric vehicles cannot use waste heat to heat the cabin and battery pack. Therefore, in electric vehicles, all heating activities need to be completed through heating and energy sources. Therefore, how to improve the utilization of the remaining energy of the vehicle becomes an electric A major issue with automotive thermal management systems.
The electric vehicle thermal management system regulates the temperature of various parts of the vehicle by managing the flow of heat, mainly including the temperature control of the vehicle motor, battery and cockpit. The battery system and the cockpit need to consider two-way adjustment of cold and heat, while the motor system only needs to consider heat dissipation. Most of the early thermal management systems of electric vehicles were air-cooled heat dissipation systems. This type of thermal management system took the temperature adjustment of the cockpit as the main design goal of the system, and rarely considered the temperature control of the motor and battery, wasting the power of the three-electric system during operation. heat generated in. As the power of the motor and battery increases, the air-cooled heat dissipation system can no longer meet the basic thermal management needs of the vehicle, and the thermal management system has entered the era of liquid cooling. The liquid cooling system not only improves the heat dissipation efficiency, but also increases the battery insulation system. By controlling the valve body, the liquid cooling system can not only actively control the direction of heat, but also make full use of the energy inside the vehicle.
The heating of the battery and the cockpit is mainly divided into three heating methods: temperature coefficient (PTC) thermistor heating, electric heating film heating and heat pump heating. Due to the chemical characteristics of the power battery of electric vehicles, there will be problems such as cold car power loss, short cruising range, and reduced charging power under low temperature conditions. In order to ensure that electric vehicles can achieve suitable working conditions under various extreme conditions, To meet the needs of use, the battery thermal management system needs to be improved and optimized for low temperature conditions.
Battery cooling method
According to different heat transfer media, the battery thermal management system can be divided into three types: air medium thermal management system, liquid medium thermal management system and phase change material thermal management system, and the air medium thermal management system can be divided into natural cooling system and air cooling system. There are 2 types of cooling system.
PTC thermistor heating needs to arrange PTC thermistor heating unit and insulating coating around the battery pack. When the vehicle battery pack needs to be heated, the system energizes the PTC thermistor to generate heat, and then blows air through the PTC through a fan(PTC Coolant Heater/PTC Air Heater). The thermistor heating fins heat it, and finally guide the hot air into the battery pack to circulate inside, thereby heating the battery.
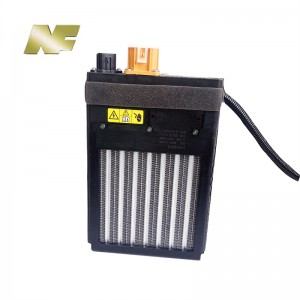
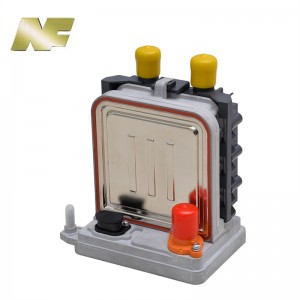
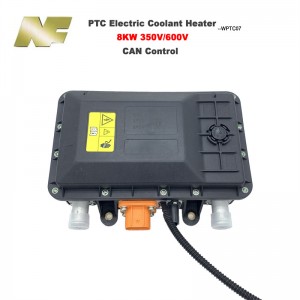
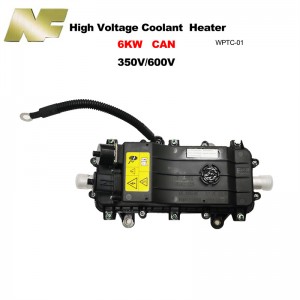
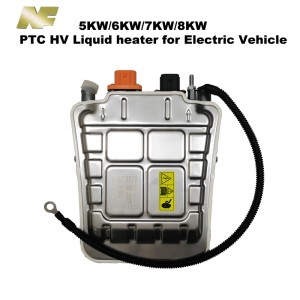
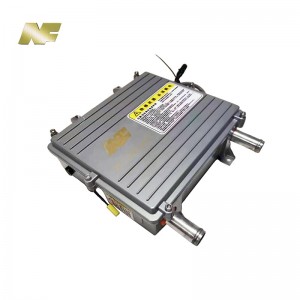
Post time: May-19-2023