1. Characteristics of lithium batteries for new energy vehicles
Lithium batteries mainly have the advantages of low self-discharge rate, high energy density, high cycle times, and high operating efficiency during use. Using lithium batteries as the main power device for new energy is equivalent to obtaining a good power source. Therefore, in the composition of the main components of new energy vehicles, the lithium battery pack related to the lithium battery cell has become its most important core component and the core part that provides power. During the working process of lithium batteries, there are certain requirements for the surrounding environment. According to the experimental results, the optimum working temperature is kept at 20°C to 40°C. Once the temperature around the battery exceeds the specified limit, the performance of the lithium battery will be greatly reduced, and the service life will be greatly reduced. Because the temperature around the lithium battery is too low, the final discharge capacity and discharge voltage will deviate from the preset standard, and there will be a sharp drop.
If the ambient temperature is too high, the probability of thermal runaway of the lithium battery will be greatly enhanced, and the internal heat will gather at a specific location, causing serious heat accumulation problems. If this part of the heat cannot be exported smoothly, along with the extended working time of the lithium battery, the battery is prone to explosion. This safety hazard poses a great threat to personal safety, so lithium batteries must rely on electromagnetic cooling devices to improve the safety performance of the overall equipment when working. It can be seen that when researchers control the temperature of lithium batteries, they must rationally use external devices to export heat and control the optimal working temperature of lithium batteries. After the temperature control reaches the corresponding standards, the safe driving target of new energy vehicles will hardly be threatened.
2. Heat generation mechanism of new energy vehicle power lithium battery
Although these batteries can be used as power devices, in the process of actual application, the differences between them are more obvious. Some batteries have greater disadvantages, so new energy vehicle manufacturers should choose carefully. For example, the lead-acid battery provides sufficient power for the middle branch, but it will cause great damage to the surrounding environment during its operation, and this damage will be irreparable later. Therefore, in order to protect ecological security, the country has put Lead-acid batteries are included in the banned list. During the development period, nickel-metal hydride batteries have obtained good opportunities, the development technology has gradually matured, and the scope of application has also expanded. However, compared with lithium batteries, its disadvantages are slightly obvious. For example, it is difficult for ordinary battery manufacturers to control the production cost of nickel-metal hydride batteries. As a result, the price of nickel-hydrogen batteries in the market has remained high. Some new energy vehicle brands that pursue cost performance will hardly consider using them as auto parts. More importantly, Ni-MH batteries are far more sensitive to ambient temperature than lithium batteries, and are more likely to catch fire due to high temperatures. After multiple comparisons, lithium batteries stand out and are now widely used in new energy vehicles.
The reason why lithium batteries can provide power for new energy vehicles is precisely because their positive and negative electrodes have active materials. During the process of continuous embedding and extraction of materials, a large amount of electric energy is obtained, and then according to the principle of energy conversion, the electric energy and kinetic energy To achieve the purpose of interchange, thus delivering a strong power to the new energy vehicles, can achieve the purpose of walking with the car. At the same time, when the lithium battery cell undergoes a chemical reaction, it will have the function of absorbing heat and releasing heat to complete energy conversion. In addition, the lithium atom is not static, it can move continuously between the electrolyte and the diaphragm, and there is polarization internal resistance.
Now, the heat will also be released appropriately. However, the temperature around the lithium battery of new energy vehicles is too high, which can easily lead to the decomposition of the positive and negative separators. In addition, the composition of the new energy lithium battery is composed of multiple battery packs. The heat generated by all the battery packs far exceeds that of the single battery. When the temperature exceeds a predetermined value, the battery is extremely prone to explosion.
3. Key technologies of battery thermal management system
For the battery management system of new energy vehicles, both at home and abroad have given a high degree of attention, launched a series of research, and has obtained a lot of results. This article will focus on the accurate evaluation of the remaining battery power of the new energy vehicle battery thermal management system, battery balance management and key technologies applied in the thermal management system.
3.1 Battery thermal management system residual power assessment method
Researchers have invested a lot of energy and painstaking efforts in SOC evaluation, mainly using scientific data algorithms such as ampere-hour integral method, linear model method, neural network method and Kalman filter method to do a large number of simulation experiments. However, calculation errors often occur during the application of this method. If the error is not corrected in time, the gap between the calculation results will become larger and larger. In order to make up for this defect, researchers usually combine the Anshi evaluation method with other methods to verify each other, so as to obtain the most accurate results. With accurate data, researchers can accurately estimate the discharge current of the battery.
3.2 Balanced management of battery thermal management system
The balance management of the battery thermal management system is mainly used to coordinate the voltage and power of each part of the power battery. After different batteries are used in different parts, the power and voltage will be different. At this time, balance management should be used to eliminate the difference between the two. Inconsistency. Currently the most widely used balance management technique
It is mainly divided into two types: passive equalization and active equalization. From the perspective of application, the implementation principles used by these two types of equalization methods are quite different.
(1) Passive balance. The principle of passive equalization utilizes the proportional relationship between battery power and voltage, based on the voltage data of a single string of batteries, and the conversion of the two is generally achieved through resistance discharge: the energy of a high-power battery generates heat through resistance heating, Then dissipate through the air to achieve the purpose of energy loss. However, this equalization method does not improve the efficiency of battery use. In addition, if the heat dissipation is uneven, the battery will be unable to complete the task of battery thermal management due to the problem of overheating.
(2) Active balance. Active balance is an upgraded product of passive balance, which makes up for the disadvantages of passive balance. From the point of view of the realization principle, the principle of active equalization does not refer to the principle of passive equalization, but adopts a completely different new concept: active equalization does not convert the electric energy of the battery into heat energy and dissipates it, so that the high energy is transferred The energy from the battery is transferred to the low energy battery. Moreover, this kind of transmission does not violate the law of energy conservation, and has the advantages of low loss, high use efficiency, and quick results. However, the composition structure of the balance management is relatively complicated. If the balance point is not properly controlled, it may cause irreversible damage to the power battery pack due to its excessive size. To sum up, both active balance management and passive balance management have disadvantages and advantages. In specific applications, researchers can make choices according to the capacity and number of strings of lithium battery packs. Low-capacity, low-number lithium battery packs are suitable for passive equalization management, and high-capacity, high-number power lithium battery packs are suitable for active equalization management.
3.3 The main technologies used in the battery thermal management system
(1) Determine the optimal operating temperature range of the battery. The thermal management system is mainly used to coordinate the temperature around the battery, so in order to ensure the application effect of the thermal management system, the key technology developed by researchers is mainly used to determine the working temperature of the battery. As long as the battery temperature is kept within an appropriate range, the lithium battery can always be in the best working condition, providing sufficient power for the operation of new energy vehicles. In this way, the lithium battery performance of new energy vehicles can always be in excellent condition.
(2) Battery thermal range calculation and temperature prediction. This technology involves a large number of mathematical model calculations. The scientists use corresponding calculation methods to obtain the temperature difference inside the battery, and use this as a basis to predict the possible thermal behavior of the battery.
(3) Selection of heat transfer medium. The superior performance of the thermal management system depends on the choice of heat transfer medium. Most of the current new energy vehicles use air/coolant as the cooling medium. This cooling method is simple to operate, low in manufacturing cost, and can well achieve the purpose of battery heat dissipation.(PTC Air Heater/PTC Coolant Heater)
(4) Adopt parallel ventilation and heat dissipation structure design. The ventilation and heat dissipation design between the lithium battery packs can expand the flow of air so that it can be evenly distributed among the battery packs, effectively solving the temperature difference between the battery modules.
(5) Fan and temperature measurement point selection. In this module, researchers used a large number of experiments to do theoretical calculations, and then used fluid mechanics methods to obtain fan power consumption values. Afterwards, researchers will use finite elements to find the most suitable temperature measurement point in order to accurately obtain battery temperature data.
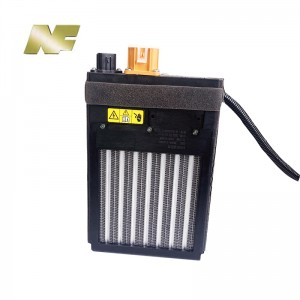
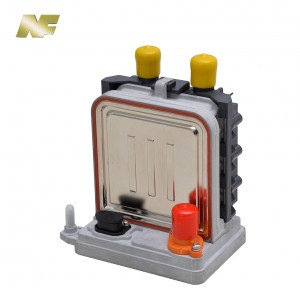
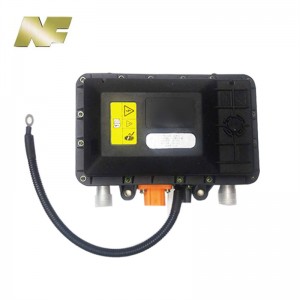
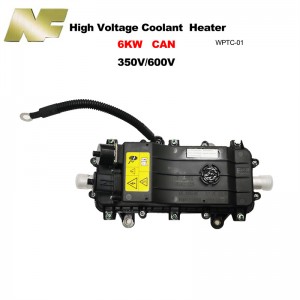
Post time: Jun-25-2023