1.Electric Vehicle Thermal Management Requirements(HVCH)
The passenger compartment is the environmental space where the driver lives while the vehicle is running. In order to ensure a comfortable driving environment for the driver, the thermal management of the passenger compartment needs to control the temperature, humidity, and air supply temperature of the vehicle interior environment. The thermal management requirements of the passenger compartment under different conditions are shown in Table 1.
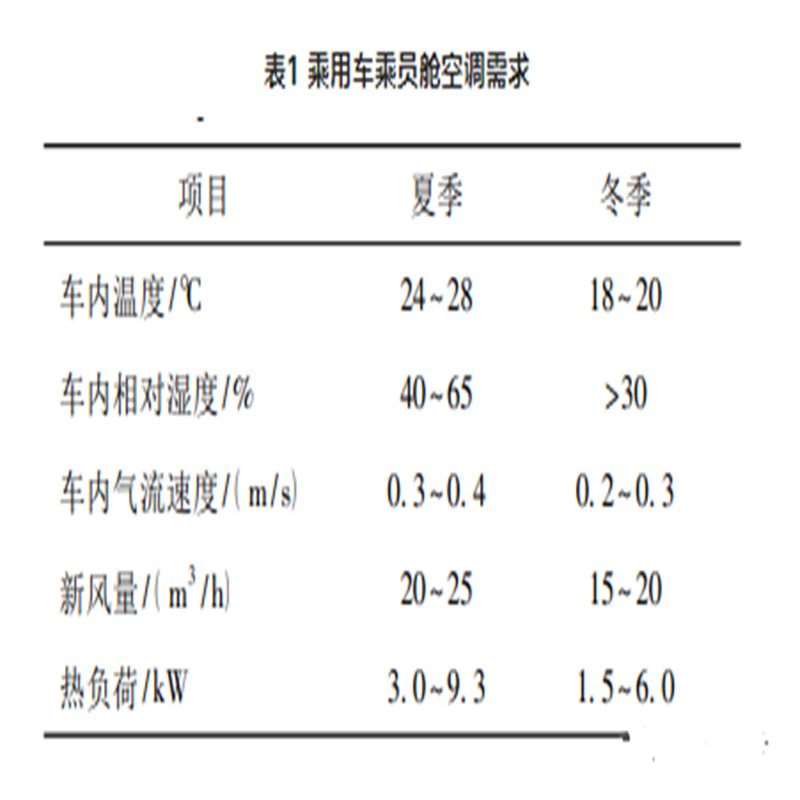
Power battery temperature control is an important prerequisite to ensure the efficient and safe operation of electric vehicles. When the temperature is too high, it will cause liquid leakage and spontaneous combustion, which will affect driving safety; when the temperature is too low, the battery charge and discharge capacity will be attenuated to a certain extent. Due to its high energy density and light weight, lithium batteries have become the most widely used power batteries for electric vehicles. The temperature control requirements of lithium batteries and the battery heat load under different conditions estimated according to the literature are shown in Table 2. With the gradual increase in the energy density of power batteries, the expansion of the temperature range of the working environment, and the increase in fast charging speeds, the importance of power battery temperature control in the thermal management system has become more prominent, not only to meet different road conditions and different charging and discharging modes. The temperature control load changes under the working conditions of the vehicle, the uniformity of the temperature field between the battery packs and the prevention and control of thermal runaway also need to meet all the temperature control requirements under different environmental conditions such as severe cold, high heat and high humidity areas, and hot summer and cold winter areas. need.
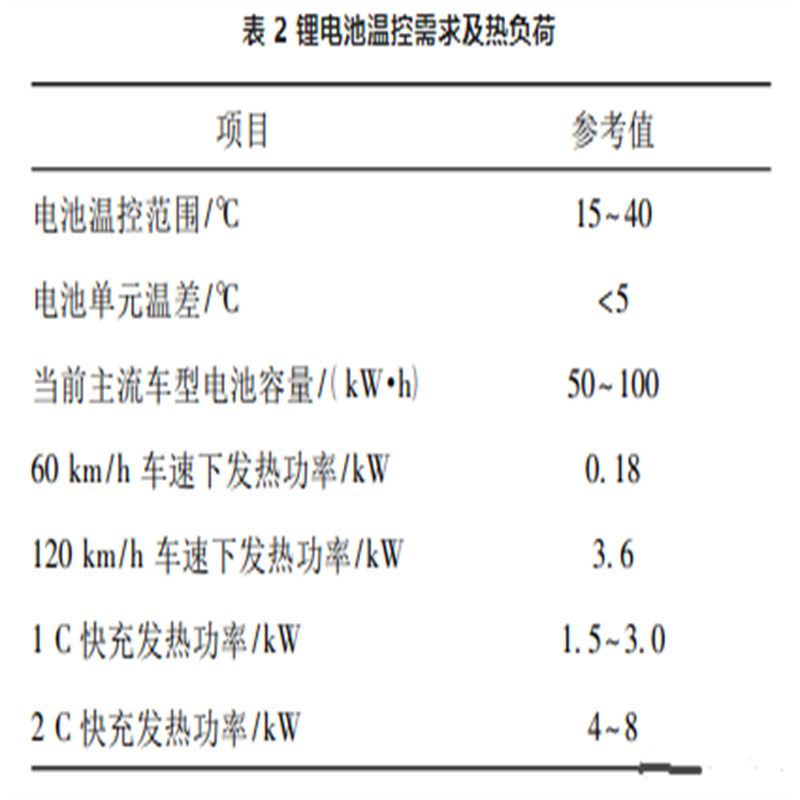
2. The first stage PTC heating
In the initial stage of the industrialization of electric vehicles, the core technology is basically based on the replacement of batteries, motors and other power systems. based on gradual improvements. The air conditioner of pure electric vehicle and the air conditioner of fuel vehicle both realize the refrigeration function through the vapor compression cycle. The difference between the two is that the air conditioner compressor of fuel vehicle is indirectly driven by the engine through the belt, while the pure electric vehicle directly uses the electric drive compressor to drive the refrigeration. cycle. When fuel vehicles are heated in winter, the waste heat of the engine is directly used to heat the passenger compartment without an additional heat source. However, the waste heat of the motor of pure electric vehicles cannot meet the needs of winter heating. Therefore, winter heating is a problem that pure electric vehicles need to solve. . Positive temperature coefficient heater (positive temperature coefficient, PTC) is composed of PTC ceramic heating element and aluminum tube (PTC Coolant heater/PTC air heater), which has the advantages of small thermal resistance and high heat transfer efficiency, and is used in the body base of fuel vehicles Therefore, early electric vehicles used vapor compression refrigeration cycle refrigeration plus PTC heating to achieve thermal management of the passenger compartment.
2.1 Application of heat pump technology in the second stage
In actual use, electric vehicles have a high demand for heating energy consumption in winter. From a thermodynamic point of view, the COP of PTC heating is always less than 1, which makes the power consumption of PTC heating high and the energy utilization rate is low, which seriously restricts electric vehicles. mileage. The heat pump technology uses the vapor compression cycle to utilize low-grade heat in the environment, and the theoretical COP during heating is greater than 1. Therefore, using a heat pump system instead of PTC can increase the cruising range of electric vehicles under heating conditions. With the further improvement of the capacity and power of the power battery, the thermal load during the operation of the power battery is also gradually increasing. The traditional air cooling structure cannot meet the temperature control requirements of the power battery. Therefore, liquid cooling has become the main method of battery temperature control. Moreover, since the comfortable temperature required by the human body is similar to the temperature at which the power battery works normally, the cooling requirements of the passenger compartment and the power battery can be met by connecting heat exchangers in parallel in the passenger compartment heat pump system. The heat of the power battery is indirectly taken away by the heat exchanger and the secondary cooling, and the integration degree of the thermal management system of the electric vehicle has been improved. Although the degree of integration has been improved, the thermal management system at this stage only simply integrates the cooling of the battery and the passenger compartment, and the waste heat of the battery and motor has not been effectively utilized.
Post time: Apr-04-2023