At present, global pollution is increasing day by day. Exhaust emissions from traditional fuel vehicles have aggravated air pollution and increased global greenhouse gas emissions. Energy conservation and emission reduction has become a key issue of concern to the international community(HVCH). New energy vehicles occupy a relatively high share in the automotive market due to their high-efficiency, clean and non-polluting electrical energy. As the main power source of pure electric vehicles, lithium-ion batteries are widely used because of their high specific energy and long life.
Lithium-ion will generate a lot of heat in the process of working and discharging, and this heat will seriously affect the working performance and life of the lithium-ion battery. The working temperature of the lithium battery is 0~50 ℃, and the best working temperature is 20~40 ℃. The heat accumulation of the battery pack above 50 ℃ will directly affect the battery life, and when the battery temperature exceeds 80 ℃, the battery pack may explode .
Focusing on the thermal management of batteries, this paper summarizes the cooling and heat dissipation technologies of lithium-ion batteries in the working state by integrating various heat dissipation methods and technologies at home and abroad. Focusing on air cooling, liquid cooling, and phase change cooling, the current battery cooling technology progress and current technical development difficulties are sorted out, and future research topics on battery thermal management are proposed.
Air cooling
Air cooling is to keep the battery in the working environment and exchange heat through the air, mainly including forced air cooling(PTC air heater) and natural wind. The advantages of air cooling are low cost, wide adaptability, and high safety. However, for lithium-ion battery packs, air cooling has low heat transfer efficiency and is prone to uneven temperature distribution of the battery pack, that is, poor temperature uniformity. Air cooling has certain limitations due to its low specific heat capacity, so it needs to be equipped with other cooling methods at the same time. The cooling effect of air cooling is mainly related to the arrangement of the battery and the contact area between the air flow channel and the battery. A parallel air-cooled battery thermal management system structure improves the cooling efficiency of the system by changing the battery spacing distribution of the battery pack in the parallel air-cooled system.
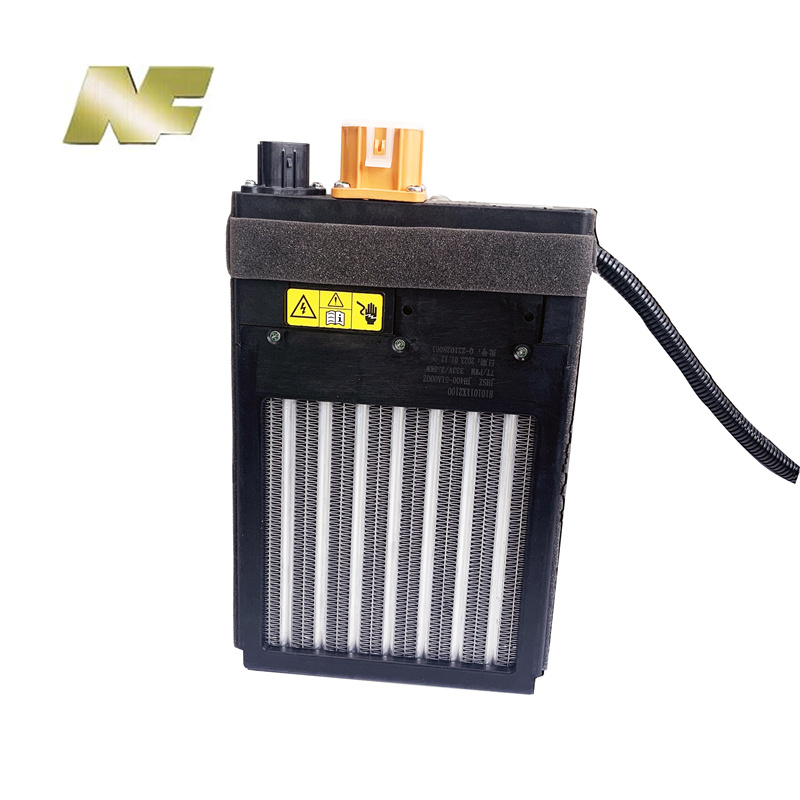
liquid cooling
The influence of the number of runners and flow velocity on the cooling effect
Liquid cooling(PTC coolant heater) is widely used in the heat dissipation of automobile batteries because of its good heat dissipation performance and the ability to maintain a good temperature uniformity of the battery. Compared with air cooling, liquid cooling has better heat transfer performance. Liquid cooling achieves heat dissipation by flowing the cooling medium in the channels around the battery or by soaking the battery in the cooling medium to take away heat. Liquid cooling has many advantages in terms of cooling efficiency and energy consumption, and has become the mainstream of battery thermal management. At present, liquid cooling technology is used in the market such as Audi A3 and Tesla Model S. There are many factors that affect the effect of liquid cooling, including the effect of liquid cooling tube shape, material, cooling medium, flow rate and pressure drop at the outlet. Taking the number of runners and the length-to-diameter ratio of the runners as variables, the influence of these structural parameters on the cooling capacity of the system at a discharge rate of 2 C was studied by changing the arrangement of the runner inlets. As the height ratio increases, the maximum temperature of the lithium-ion battery pack decreases, but the number of runners increases to a certain extent, and the temperature drop of the battery also becomes smaller.
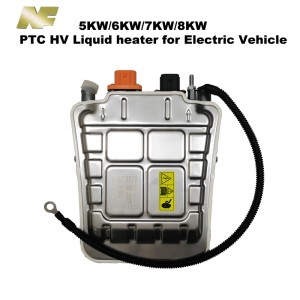
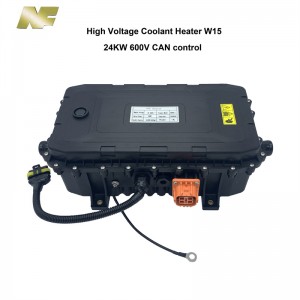
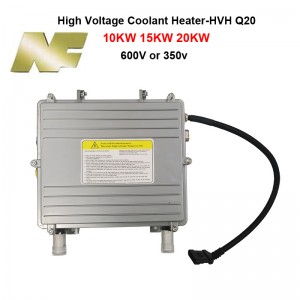
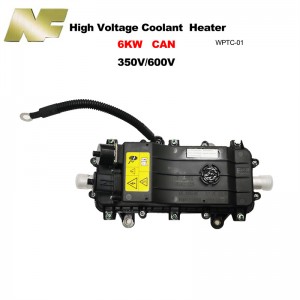
Post time: Apr-07-2023