There is no doubt that the temperature factor has a crucial impact on the performance, life and safety of power batteries. Generally speaking, we expect the battery system to operate in the range of 15~35℃, so as to achieve the best power output and input, the maximum available energy, and the longest cycle life (although low temperature storage can extend the calendar life of the battery , but it does not make much sense to practice low-temperature storage in applications, and batteries are very similar to people in this regard).
At present, the thermal management of the power battery system can be mainly divided into four categories, natural cooling, air cooling, liquid cooling, and direct cooling. Among them, natural cooling is a passive thermal management method, while air cooling, liquid cooling, and direct current are active. The main difference between these three is the difference in heat exchange medium.
· Natural cooling
Free cooling has no additional devices for heat exchange. For example, BYD has adopted natural cooling in Qin, Tang, Song, E6, Tengshi and other models that use LFP cells. It is understood that the follow-up BYD will switch to liquid cooling for models using ternary batteries.
· Air Cooling (PTC Air Heater)
Air cooling uses air as the heat transfer medium. There are two common types. The first one is called passive air cooling, which directly uses external air for heat exchange. The second type is active air cooling, which can pre-heat or cool the outside air before entering the battery system. In the early days, many Japanese and Korean electric models used air-cooled solutions.
· Liquid cooling
Liquid cooling uses antifreeze (such as ethylene glycol) as the heat transfer medium. There are generally multiple different heat exchange circuits in the solution. For example, VOLT has a radiator circuit, an air conditioning circuit (PTC Air Conditioning), and a PTC circuit (PTC Coolant Heater). The battery management system responds and adjusts and switches according to the thermal management strategy. The TESLA Model S has a circuit in series with the motor cooling. When the battery needs to be heated at low temperature, the motor cooling circuit is connected in series with the battery cooling circuit, and the motor can heat the battery. When the power battery is at high temperature, the motor cooling circuit and the battery cooling circuit will be adjusted in parallel, and the two cooling systems will dissipate heat independently.
1. Gas condenser
2. Secondary condenser
3. Secondary condenser fan
4. Gas condenser fan
5. Air conditioner pressure sensor (high pressure side)
6. Air conditioner temperature sensor (high pressure side)
7. Electronic air conditioner compressor
8. Air conditioner pressure sensor (low pressure side)
9. Air conditioner temperature sensor (low pressure side)
10. Expansion valve (cooler)
11. Expansion valve (evaporator)
· Direct cooling
Direct cooling uses refrigerant (phase-changing material) as the heat exchange medium. The refrigerant can absorb a large amount of heat during the gas-liquid phase transition process. Compared with the refrigerant, the heat transfer efficiency can be increased by more than three times, and the battery can be replaced more quickly. The heat inside the system is carried away. The direct cooling scheme has been used in the BMW i3.
In addition to the cooling efficiency, the thermal management scheme of the battery system needs to consider the consistency of the temperature of all batteries. PACK has hundreds of cells, and the temperature sensor cannot detect every cell. For example, there are 444 batteries in a module of Tesla Model S, but only 2 temperature detection points are arranged. Therefore, it is necessary to make the battery as consistent as possible through thermal management design. And good temperature consistency is the prerequisite for consistent performance parameters such as battery power, life, and SOC.
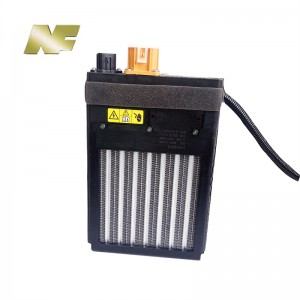
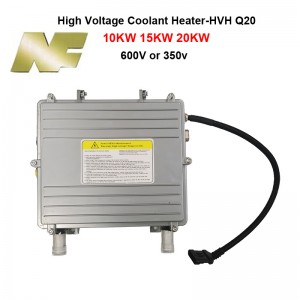
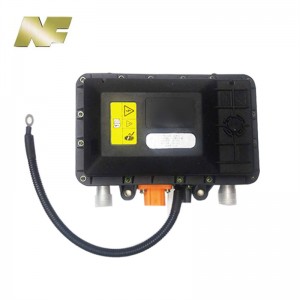
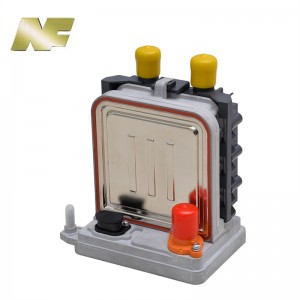
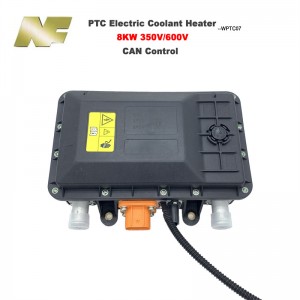
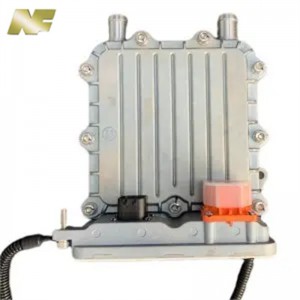
Post time: Apr-28-2024