For heat transfer with liquid as the medium, it is necessary to establish a heat transfer communication between the module and the liquid medium, such as a water jacket, to conduct indirect heating and cooling in the form of convection and heat conduction. The heat transfer medium can be water, ethylene glycol or even Refrigerant. There is also direct heat transfer by immersing the pole piece in the liquid of the dielectric, but insulation measures must be taken to avoid short circuit.(PTC Coolant Heater)
Passive liquid cooling generally uses liquid-ambient air heat exchange and then introduces cocoons into the battery for secondary heat exchange, while active cooling uses engine coolant-liquid medium heat exchangers, or electric heating/thermal oil heating to achieve primary cooling. Heating, primary cooling with passenger cabin air/air conditioning refrigerant-liquid medium.
For thermal management systems that use air and liquid as the medium, the structure is too large and complex due to the need for fans, water pumps, heat exchangers, heaters, pipelines and other accessories, and it also consumes battery energy and reduces battery power. density and energy density.(PTC Air Heater)
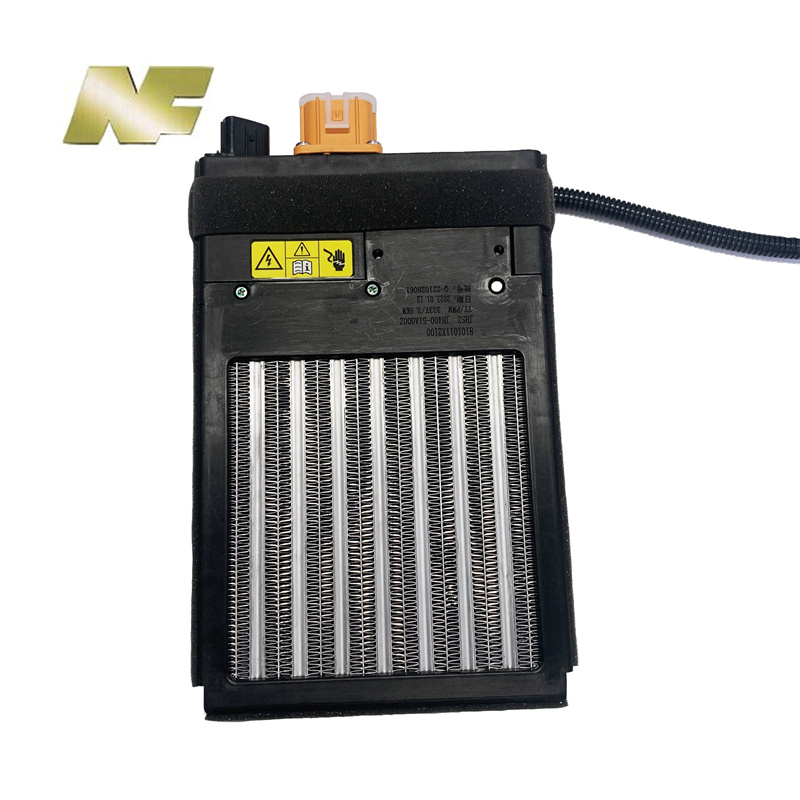
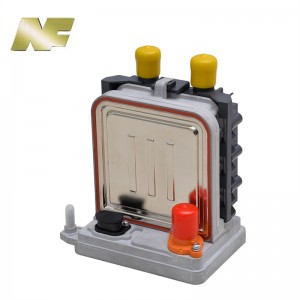
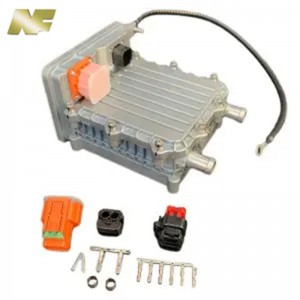
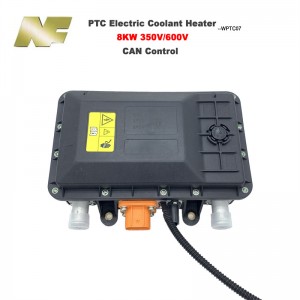
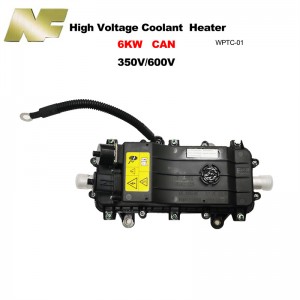
The water-cooled battery cooling system uses coolant (50% water/50% ethylene glycol) to transfer the battery heat to the air-conditioning refrigerant system through the battery cooler, and then to the environment through the condenser. The battery inlet water temperature is cooled by the battery It is easy to reach a lower temperature after heat exchange, and the battery can be adjusted to run at the best working temperature range; the system principle is shown in the figure. The main components of the refrigerant system include: condenser, electric compressor, evaporator, expansion valve with shut-off valve, battery cooler (expansion valve with shut-off valve) and air conditioning pipes, etc.; cooling water circuit includes: electric water pump, battery (including cooling plates), battery coolers, water pipes, expansion tanks and other accessories.
In recent years, battery thermal management systems cooled by phase change materials (PCM) have appeared abroad and at home, showing good prospects. The principle of using PCM for battery cooling is: when the battery is discharged with a large current, the PCM absorbs the heat released by the battery, and undergoes a phase change by itself, so that the temperature of the battery drops rapidly.
In this process, the system stores heat in the PCM in the form of phase change heat. When the battery is being charged, especially in cold weather (that is, the atmospheric temperature is much lower than the phase transition temperature PCT ), the PCM emits heat to the environment.
The use of phase change materials in battery thermal management systems has the advantages of not requiring moving parts and consuming additional energy from the battery. Phase change materials with high phase change latent heat and thermal conductivity, used in the thermal management system of the battery pack can effectively absorb the heat released during charging and discharging, reduce the temperature rise of the battery, and ensure that the battery works at a normal temperature. It can keep the battery performance stable before and after the high current cycle. Adding substances with high thermal conductivity to paraffin to make composite PCM helps to improve the overall performance of the material.
From the perspective of the above three types of thermal management forms, phase change heat storage thermal management has unique advantages, and it is worthy of further research and industrial development and application.
In addition, from the point of view of the two links of battery design and thermal management system development, the two should be organically combined from a strategic height and developed synchronously, so that the battery can better adapt to the application and development of the whole vehicle, which can save the cost of the whole vehicle , and can reduce the application difficulty and development cost, and form a platform application, thereby shortening the development cycle of new energy vehicles and speeding up the marketization progress of different new energy vehicles.

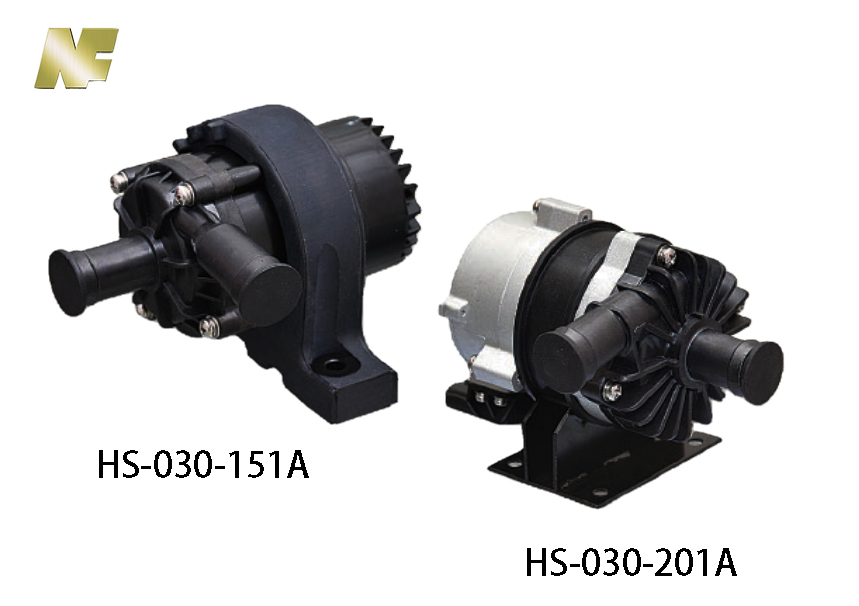
Post time: Apr-27-2023